Masahira Fujiyasu, a swordsmith who has Masahira Forge in Fukushima City, Fukushima Prefecture and makes Japanese swords. Mr. Munehiro Shibata, a bow store owner in Kyoto for 500 years, told me, “There is an interesting person who makes Japanese swords in Fukushima Prefecture, and I will introduce him to you.” As I headed to Mr. Fujiyasu’s workshop, I heard the sound of steel being pounded. We asked him, who has been making Japanese swords for more than 50 years, about his background and vision for the future.

- ―When did you first become interested in making things?
-
I think since I was born! It was not an interest or anything, but the act of making something was a natural part of my daily life, so I was making various things from a young age. When he was little, if he found a tree branch, he would shape it like a sword to play. Toys were not sold in those days, so he made toys by himself. It was more fun to make the tools than to enjoy playing the game.
- ―So you have had a close relationship with crafting since your childhood. What was it that inspired you to pursue a career in Japanese sword making?
-
When I was in high school, I read a book by living national treasure, Yukihira Miyairi, titled “A Master Sword Maker’s Life. I was surprised to know that there are people who still make Japanese swords today. I was so surprised that I couldn’t stop myself from wanting to see one in person. At the end of the book, it says, “I hope there will be even one young person to whom I can entrust my own feelings. I thought it is about me!
I was thinking to take over the family business, so I did not even think about job hunting. However, it was not possible to watch videos of Japanese sword making on YouTube as is the case today, nor was it possible to contact the author by e-mail. At the time, job opportunities were hard to come by, and I was able to find a job in Nagano Prefecture, where the author (Yukihira Miyairi) was located, so I moved to there. On my first day off, I went to see him at work and was so happy to see him working all day long, the atmosphere, the sounds, the smells, the movements, everything was amazing. After that, I went to the work place many times, but my master did not even remember my name and kept refusing to take me on as an apprentice. I was a very small young man weighing only 48 kg at the time, so I felt it was inevitable. But I continued to go to work, and the master’s wife asked him, “Why don’t you let him help my work and take him as my apprentice?” So at first, I was not the master’s apprentice, but his wife’s apprentice (laugh).

- ―You were an apprentice of your master’s wife. How did you become the master’s apprentice from there?
-
I could not become a master’s apprentice right away. He didn’t even remember my name, and I didn’t have the physical strength to do it myself in the first place. Still, I thought every day about what I could do to stay here anyway. I thought of practiced appealing methods to get out of the repetitive life of cooking dinner, playing with the master’s daughter, taking a bath, and going to bed. I woke up at 5:00 a.m. and practiced swinging the heavy large hammer used for making swords toward the roots of trees to build up my physical strength, and one day, I imagined striking the steel straight in the process of evenly splitting wood for burning charcoal. After spending such days, on rare occasions, my master would call me and ask me to beat steel. Then, my master gave me a work uniform and I became his apprentice.
At first glance, it looks like I was able to become an apprentice because I had practiced hard and so on, but the real reason was something else. The real reason, he told me, was just because I cleaned the gas table really well. At the time, I was not getting any work and had a lot of time, so I used to clean the whole house. The gas table was very dirty, so I got a whetstone from the workplace and cleaned it. The master thought that even though he was small, this guy might be able to handle it because he not only cleaned the dirt and made it clean, but also pursued “beauty”.
Now I really understand that the “beauty” that the master was pursuing settles not only in Japanese swords but also in all Japanese objects. During the six months I was apprenticed to the master’s wife, I had no assurance that I would become his apprentice as a sword smith, but it was a very happy moment for me that I kept doing what I was supposed to do.

- ―And from there you were finally able to enter the field?
-
No, I still could not enter the field from there either. I was working at the edge of the workshop, cutting charcoal. My master said, “Hey!” and the brother would approach and strike the steel at the right moment. I simulated the flow hundreds of times while working at the edge cutting charcoal, asking myself, “Is this the right time to go?
I tried many times to place the coals on the route where the brother and sister would be called by the master, even cunningly, and I eagerly awaited the day when I would be called upon to do so. Then one day, the brother was in bad condition and the big hammer did not hit the steel, and eventually broke the steel. The master became impatient and said, “Take over!” and it was my turn. I got that one shot right, and from then on, the number of times I was called in for that routine increased. - ―I see that your work has been busy since then. When did you make your first sword?
-
Seven years after I became an apprentice, I finished my first sword by myself. I received an award for this one, which gave me confidence in myself. What made me more happy than winning the award was when I learned that my master, who did not usually give me compliments, was spreading the word to the people around him, saying, “Fujiyasu made a good sword.”

- ―When did you become independent, Mr. Fujiyasu?
-
Eleven years after starting to work for my master. To be honest, I did not intend to become independent at that time. I wanted to pursue the beauty of real Japanese swords, so I wanted to build a sword laboratory near my master’s factory and have my master make swords based on the results of my research.
However, when I was 30 years old, my vision turned white and I became blind due to overwork. I was under the care of a doctor I knew for a while, and suddenly I fell down the stairs. That moment made me see things again, and when I returned to my master’s place with that foot, he told me to go back to my parents’ house and prepare to start my own business because you never rest if you work here, and that’s how I became independent. - ―So you didn’t plan to be independent from the beginning. Have you been working here since you became independent?
-
Yes, I have been based here. When I first became independent, I went to Nagano Prefecture every month. Every time I met my master, I learned something new and was inspired. Not long after I became independent, my master collapsed at his workplace. At the time, I didn’t think it was very sad. I rather thought that I would like to die in the workplace like this too. But now, on the contrary, I strongly wish to live longer. I am going to do my best to nurture the apprentices I have now. I have to work hard for another 30 years (laughs).
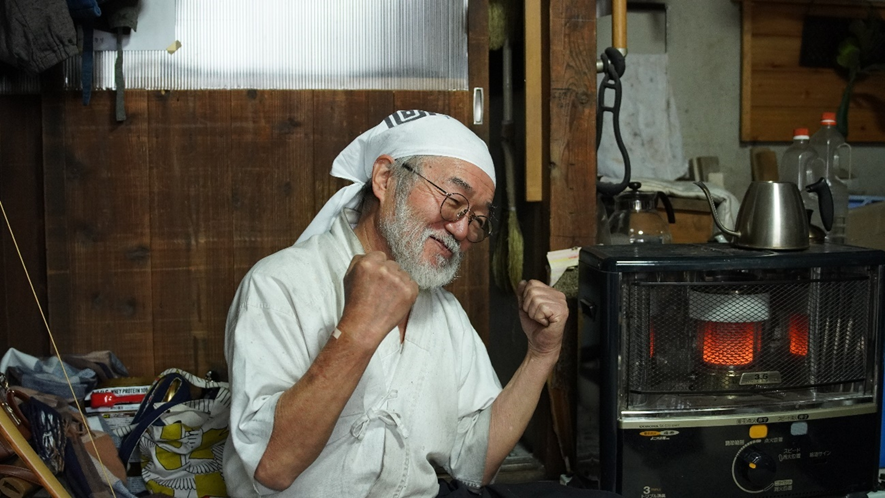
- ―What has been etched in your mind after spending 11 years with your master?
-
There are two things: First thing is to do things until you are satisfied with them. Second is to do whatever you want, but the question is whether it is beautiful or not. As I mentioned earlier, with a Japanese sword, it is not enough just to cut it. I want to pursue beauty from multiple perspectives, such as how beautiful it looks and whether or not it makes people think it can cut and create a form that I am satisfied with.
- ―What is your main concern when making a sword?
-
It is very difficult to put into words, but I think it is “to leave no trace of having been made by human.” I want to create something that is close to nature. Mountains, oceans, skies and other natures are all things that we humans find beautiful. I am particular about how I can bring it closer to those things. I want the sword to exist in nature just as a flower blooms and withers. When you look at old swords, there is no doubt that they were made by people, but strangely enough, they have a beauty as if they were created naturally.
Especially in today’s society, all goods are made with very advanced techniques, and the creator’s awareness of making them is so strong that it is tiring to watch. To be honest, I find it boring. The temperature, humidity, quality of the charcoal, and the expression of the fire are all different depending on the season, and the Japanese sword is made under different conditions. It is fun to see how beautiful a sword can be made under these different conditions, and I think our customers enjoy it as well.
I think the bows made at Shibata Kanjuro Bow Shop are the same case. There is no such thing as 100% identical conditions for the bamboo used to make a bow, and I think that we look at the expression of the material and see what the material wants to be while we are dealing with it. Once, when Munehiro was driving a wedge, Kanjuro (22nd generation) said to him, “Drive three more!” and I thought, “What difference does three strokes make?” But if you ask Mr. Kanjuro the reason for those three strokes, I don’t think he can explain it. I think it would come down to the senses that he has cultivated over the years. Therefore, I guess my commitment is to pursue “beauty” that cannot be put into words and create natural Japanese swords.
- ―Finally, Mr. Fujiyasu, could you give a message to the youth?
-
I think you should live the life you want and do what you want, considering that the responsibility is all yours!!!
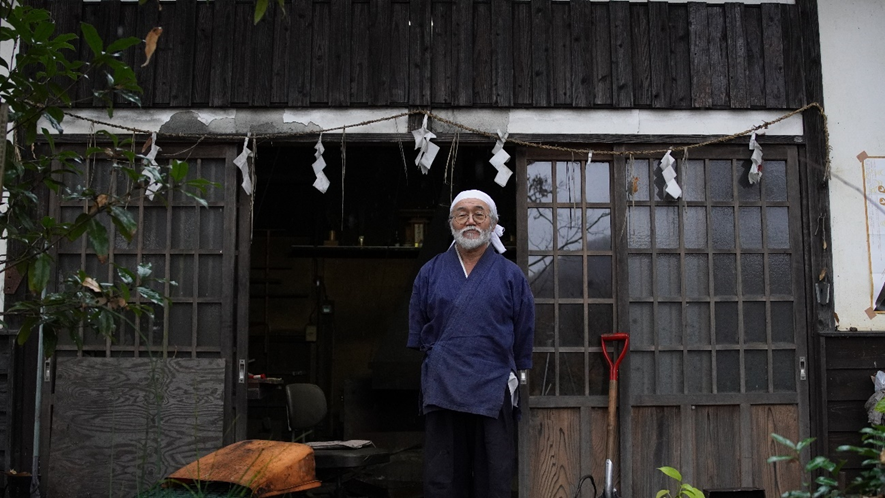
After the interview
After the interview and chatting with Mr. Fujiyasu, we found a lot of manga on the bookshelf at the factory. Mr. Fujiyasu’s current favorite is “The Fable” a story about an assassin. The main character, Fable, makes everything, even guns, by sourcing natural materials. “You can learn a lot from manga.”, he said. He lent us all the comic books. When I read Fable in my free time, it reminds me of Mr. Fujiyasu. And I think I am gradually beginning to understand why he likes this manga so much.
He creates things by hands and the beauty of forms that seem to have originally existed in the natural world. I feel that the interview with Mr. Fujiyasu taught me the essence of craftsmen who have chosen to master the art of making things. I feel that we should also strive to support craftspeople like Mr. Fujiyasu with a sense of mission.
Japanese swords made by Mr. Fujiyasu can be purchased from special-ordered from the Suigenkyo online store. Please feel free to contact us as Suigenkyo staff will be happy to assist you with your request.
You can watch the making process on YouTube!