Kato Cloisonne Works has a workshop in Nagoya City, Aichi Prefecture. I interviewed Mr. Yoshiro Kato, the third president of the company. Mr. Kato, who was certified as a national traditional craftsman in 2018, said he loves his workshop, which is covered with orange color in the evening when the sun shines in the west and has a nostalgic look. We asked Mr. Kato, whose passion for cloisonne enamel ware was overflowing even before the interview, about his background and future vision for Kato Cloisonne Cloisonne Jewelry.
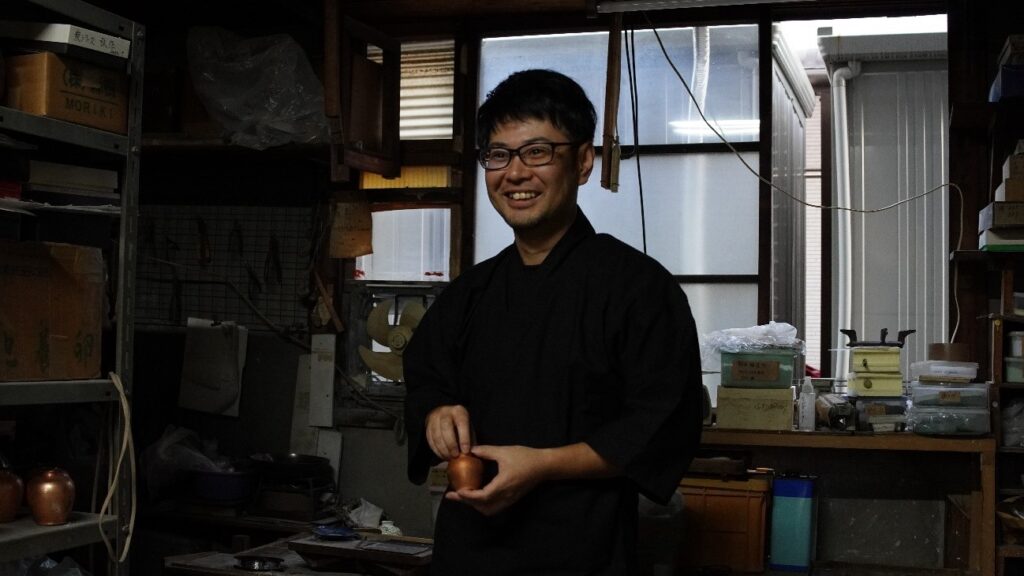
- —How were you interested in crafting things?
-
It was a time I experienced repairing video game consoles by myself when I was a child. Unlike today’s game consoles, old ones could be taken to pieces easily. As a child, I had the idea that I wanted to look inside and maybe I could repair it. I could eventually fix it. When I took it apart and cleaned it, I could see things that I had not seen before. Then I began to wonder what was inside. From there, I got into plastic models, mini 4-wheelers, and radio-controlled cars, and I enjoyed thinking about how to make them faster and lighter by modifying them in my own way.
- —You must have been very into it to the extent that you spent all of your New Year’s money.
-
At that time, I was really into cars. It was a time when F1 was on TV, and I was a big fan of it.
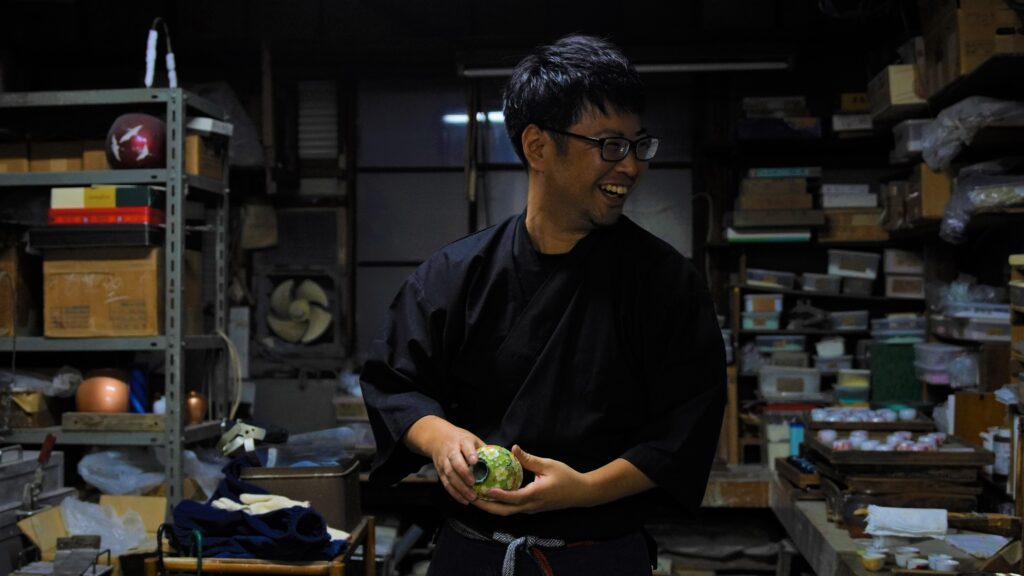
- —How did you start your career path?
-
I entered a design university as I wanted to learn about manufacturing and design from all a perspective. At the university, I learned not only about the fields in which I was interested, but also about design in general. I believe that all the practical skills and lectures I learned at that time have been useful for product development at Kato Cloisonne Works today.
- —When I heard about it from you, I thought that you are more interested in the electrical and engineering fields, which are different from your current work. When did you start to interest in Cloisonne crafts?
-
I was actually interested in the Cloisonne crafts at the third year of my college, when I was deciding where to work. Actually, I wanted to be a modeler, which is a profession that involves designing cars. As a car lover, working for designing a car made me think that this was exactly the kind of job I wanted to do. I was also attracted by butterfly stools at Tendo Woodworking and dreaming if I can make one of these one day. I had no intention of taking over the family business at the time.
- —What happened during your third year of college?
-
I was looking for a job in the field of making things, and I was faced with the dilemma of whether I should not turn my attention to the family business, even though I was considering to work as a modeler or furniture maker. However, while I was looking for a job, I could not ignore the option of taking over the family business. I was driven to a situation where I had to be clear, so I decided to research about cloisonne first, and I did a crazy amount of research. There I came across the works of Yasuyuki Namikawa, and I decided to pursue cloisonne enamel art. I was amazed at the difference between the cloisonne enamel works I had seen at home and those of the Meiji when Namikawa was still alive. I was so impressed by their beauty and I visited the Sannenzaka Museum of Art in Kyoto and the Yasuyuki Namikawa Cloisonne Enamels Memorial Museum in person to see his works. I felt depressed when I knew that the cloisonne enamel industry was facing difficult moment, despite the fact that such detailed, precise, and beautiful works could be made with silver wire and glaze. I thought that I would regret for the rest of my life if I chose not to do cloisonne work because there was still a chance to make cloisonne work with my family business.
- —You had a dilemma in deciding to take over the family business. What were your honest thoughts when you finally joined the family business?
-
When I first joined the company, I spent every day struggling to master a set of skills. IfI look back, it took me about 5 years to acquire the minimum skills, and 10 years to be regarded as a full-fledged professional. It was a harder road than I had imagined, and I continue to do it every day because there is no end to the study of technology. However, at that time, in addition to improving my own skills, I felt the importance of “sharing information”. I thought it would be a waste if people who were interested in Owari Cloisonne did not have access to proper information. So shortly after I joined the company, I started to create a website for the company, and it took more than two years to launch it with the help of my friends.
- —It is difficult to engage with SNS, isn’t it? Is there anything you want to try with SNS strategy?
-
Rather than having a specific strategy, I would like to carefully deliver right information. Recently, fake news has been shared on social networking services, and I believe that we are living in an era in which its literacy is being questioned. From this circumstance, I am conscious of delivering accurate information to everyone. In today’s information society, even information that is posted today will quickly become outdated and buried in the next 24 hours. From now on, I would like to focus on the ability to continuously share information that can be seen through SNS and to increase the number of fans through events and collaborations!
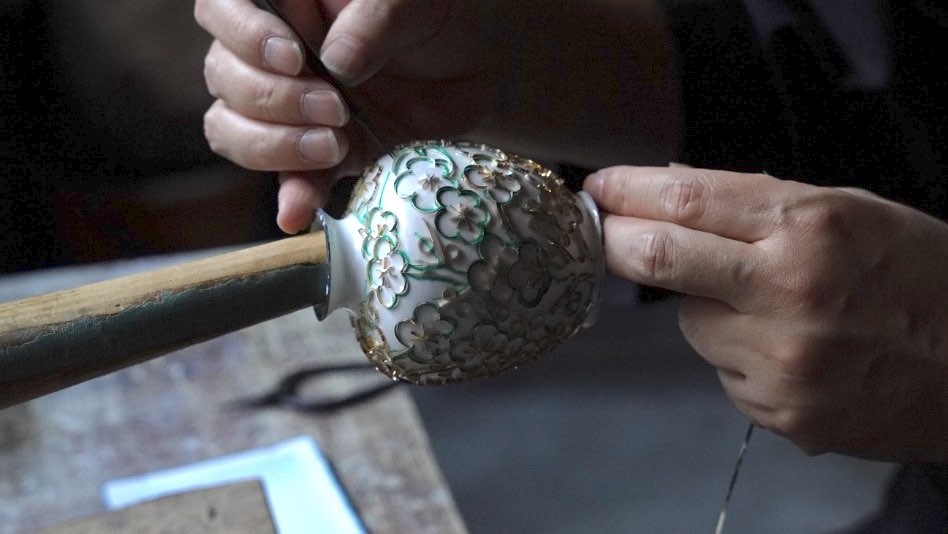
- —What do you think is the attractiveness of Owari cloisonne in your opinion?
-
It can be the beauty and delicate of the craft. You can create all kinds of design with a single silver wire. Its glazed look cannot be seen in any other crafts! There was a time a long time ago when making large objects was right thing to do, but the craft I am aiming to make is “the ultimate beauty that fits in the palm of your hand. In Namikawa’s time, as I mentioned earlier, it took a year to create one piece of artwork, and it was said that a house could be built with just one piece of artwork. I find it precious that an amazing amount of work is packed into a craft with the size of the palm of your hand. I would like to make a piece of work that will allow people to feel even a small part of that era through my work. Personally, I would like to remake Namikawa’s work! It would be very presumptuous of me to even mention it (laughs).
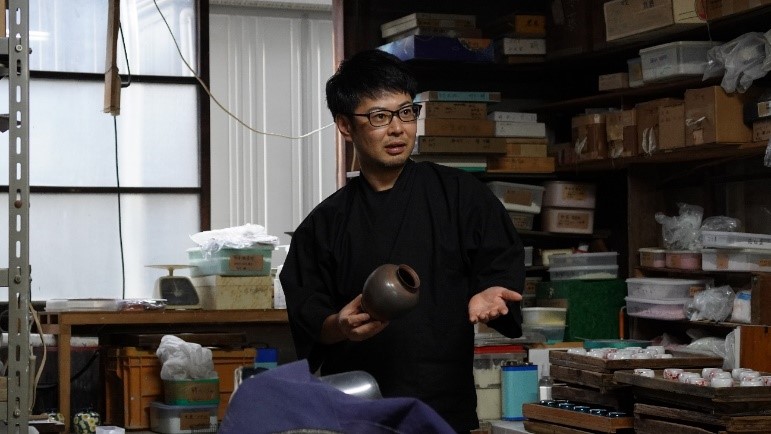
- —Lastly, please tell us about your future vision for Kato Cloisonne Works!
-
As I have been doing steadily in the past, I would like to find a way toward a better future by actively engaging with people from various fields as much as possible.
Although we may be in different positions and specialize in different fields, we all have overlapping thoughts and new insights. I believe that there are hidden hints for a better future. For example, as makers, we create appealing products and artworks, and Suigenkyo communicates and sells those appealing products and artworks to the world.
SNS is also important, not only to introduce products and works, but also to show the thoughts of the creators behind the production, the production process, and other aspects that are difficult to see only in the finished products. Owari cloisonne, in particular, has a complex production process and a variety of expressions. Since we are doing something that cannot be found anywhere else, we think we need to put even more effort into disseminating information. However, the more we concentrate on creating, the more we often miss the timing to take good photos and have a hard time later on. I feel that the challenge is how to consistently transmit information of the highest quality possible, and we are working on this while involving the people around us as much as possible and thinking about it together. I would like to cherish the relationships with people who are interested in our work, and I would like to open up new avenues for us.
After the interview
In addition to the interview, we also asked for their help to film a video of cloisonne enamel production for two days. We also asked him about his thoughts on cloisonne and the craft industry. Mr. Kato expressed his frustration, saying that although he has the desire to create a masterpiece, he has never managed to do it due to the cost of raw materials and kiln repairs. Suigenkyo’s desire is for its artisans to create masterpieces that is even more beautiful than any past masterpieces by the end of their lives. My heart was filled with excitement as we decided to do what we should do as Suigenkyo in order to create such an environment.
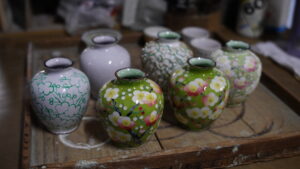